The ICD/ITKE Research Pavilion developed by a multidisciplinary team at the Institute for Computational Design. In recent years, architects, biologists, and engineers have been thinking about the possible connection the architectural field can have with living entities, such as insects or trees. Most of the time, architects design projects based on the imitation of natural forms. This imitation takes place in a field where there haven’t been previous studies about the organism being imitated, its basic organic functions, and its interaction with the environment. This concept is called biomorphism. When you add in concepts such as biomimicry and biomimetics as theoretical foundations, the design process is focused on the understanding of the functions of the project, how its functions and structure can be solved by studying a specific organism, and, in some supported research projects, how it can be built with parametric design. WATCH: Biomimicry and Landscape Architecture The ICD/ITKE Research Pavilion was developed by a multidisciplinary team at the Institute for Computational Design, which is part of the faculty of architecture and urban planning of the University of Stuttgart. The team included architects, engineers, biologists, and paleontologists. The pavilion was part of a research project focused on demonstrating the potential of novel design, simulations, and fabrication processes in architecture, based on nature and parametric design.
From Beetles to Architecture: The Design Process
Considering the context and the functions to which the pavilion would respond, architects were concerned about the living organism that can be the foundation to develop biomimetic design. All these, along with the problems that Stuttgart’s weather can cause, forced the architects to consider the study of the Elytron, a type of hardened forewing that certain types of insects possess, including beetles.

Comparison of internal elytron architecture in flying and flightless beetle. Credit: © Dr.Thomas van de Kamp, Prof. Dr. Hartmut Greven
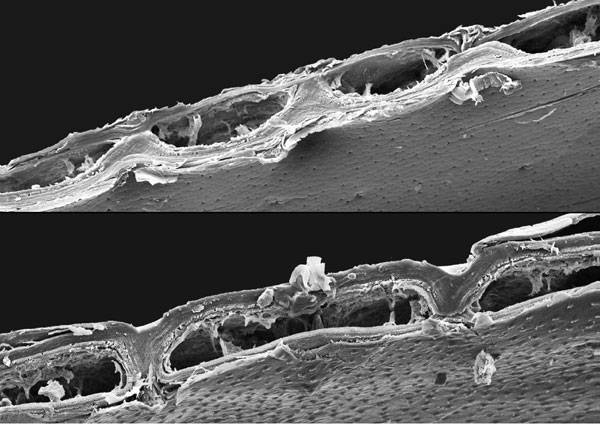
SEM scans of Potato Beetle (leptinotarsa decimlineata) elytron scanned for the ICD/ITKE Research Pavilion 2013-14 by Prof. Oliver Betz at University of Tuebingen. Credit: © Prof. Oliver Betz, Anne Buhl, University of Tübingen

Elytra cross sections based on microcomputed tomography scans for the ICD/ITKE Research Pavilion 2013-14 by Dr. Thomas van de Kamp at the ANKA Synchrotron Radiation Facility of Karlsruhe Institute of Technology (KIT) Credit: © ICD/ITKE University of Stuttgart
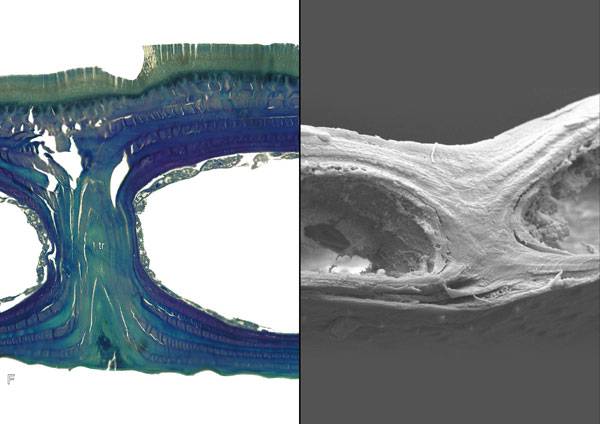
Correlation of fiber layout and structural morphology in trabeculae. Credit: © Dr. Thomas van de Kamp, Prof. Dr. Hartmut Greven | Prof. Oliver Betz, Anne Buhl, University of Tübingen
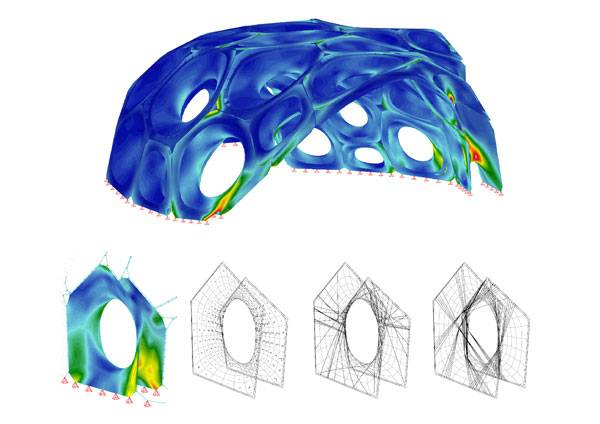
Finite element analysis of global force flows and their transfer into structural carbon fiber reinforcements. Credit: © ICD/ITKE University of Stuttgart
- Biomimicry UK: Interview with Richard James MacCowan
- Biomimicry: What is it and What Does it Mean For Landscape Architects?
- Naples Gridshell Urban Furniture Experiment
Glass and carbon fiber-reinforced polymers were chosen as construction materials for the panels, due to their unique qualities such as high strength-to-weight ratio and its potential to generate different material properties by changing its arrangement.
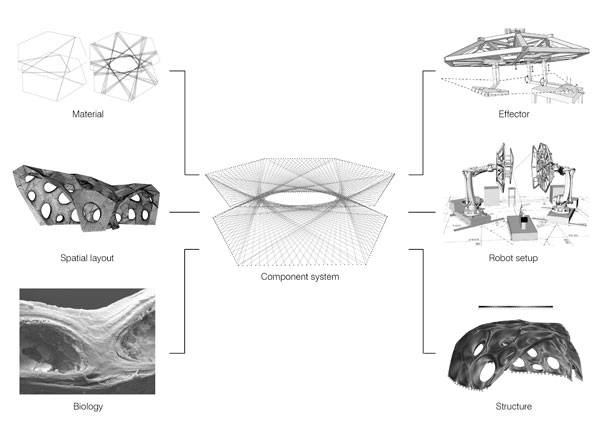
Integration of multiple process parameters into a component based construction system. Credit: © ICD/ITKE University of Stuttgart
An Attractive Organic Design
For the fabrication of the geometrically unique double-curved modules, a robotic coreless twisting method was developed, which used two collaborating 6-axis industrial robots to wrap chitin fibers between two custom-made steel frame effectors.
The interaction between fibers generates doubly curved surfaces from initially straight deposited fiber connections. These reciprocities among material, form, structure, and fabrication are defined through a winding syntax that becomes an integral part of the computational design tool.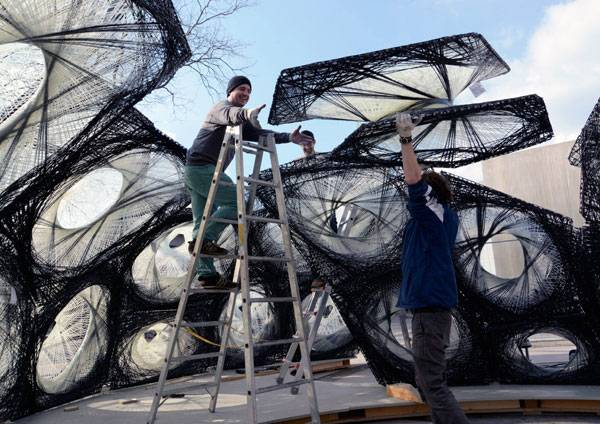
Assembly process of 36 lightweight fiber composite components on site. Credit: © ICD/ITKE University of Stuttgart
- ARCHITECTURE without architecture: Biomimicry design by Carlos Ginatta
- Discovery of Design by Donald DeYoung
Article written by Luis Eduardo Guisar Benitez Return to Homepage
Published in Blog